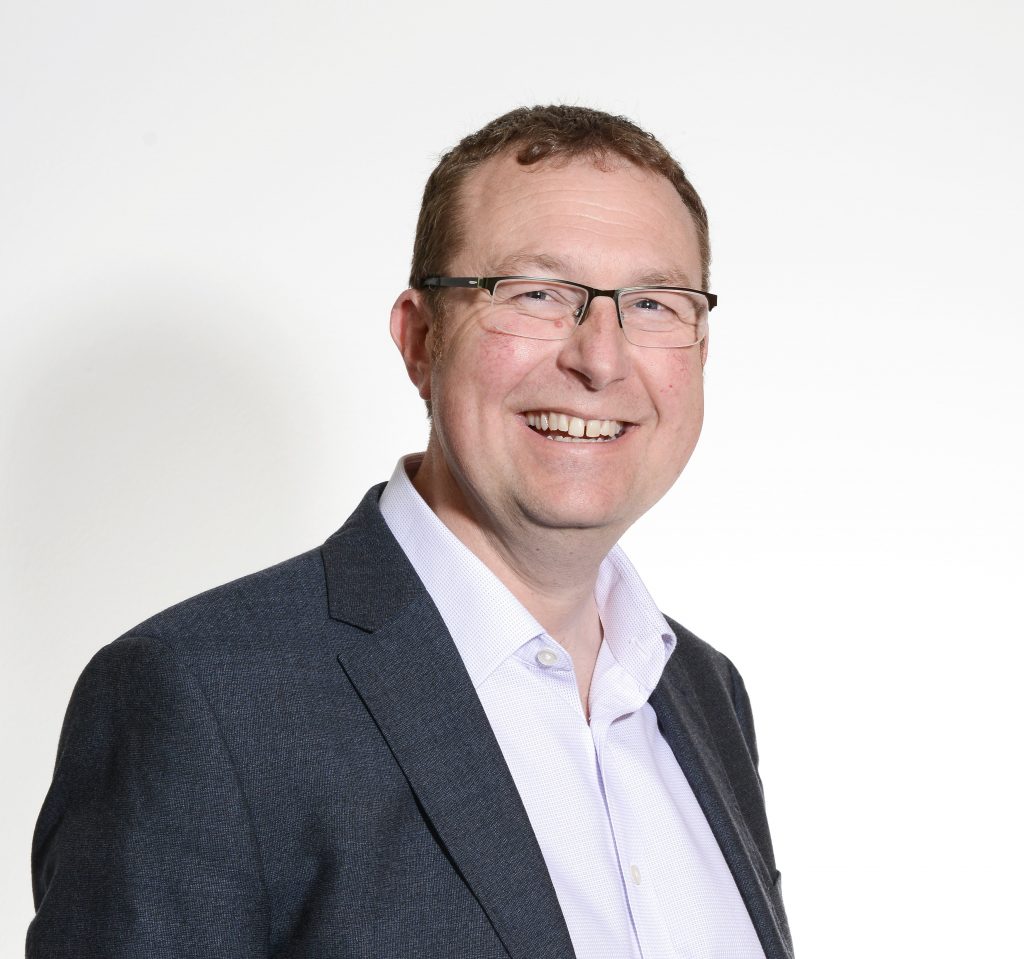
I always enjoy the industry conferences, and this year, virtually, it was as good as ever. It is very interesting for me, listening to the wider EFW community debate how projects are constructed, the perceived risks involved and the conclusion that the EPC delivery model is a challenge, often failing and that civil works are a ‘problem’ or ‘always’ the part that fails.
Chilworth specialises in civil works and principal contractor management and, with a decade of experience in the energy sector, I want to share why we think that EPCM is the answer.
We know lots of components and complicated contracts are required to develop and deliver a large energy from waste plant in the UK, with many challenges from its construction to plant performance and plant availability after takeover.
But why is construction perceived as such a challenge? With EPCM it doesn’t need to be.
This year the debate moved on again with the EPCM model attracting more credence as a way to deliver projects better, but is it? My answer is a resounding ‘YES’.
The market is changing and the benefits of EPCM are starting to come to the fore with clients and stakeholders challenging whether the current EPC model works. From Chilworth’s perspective, we rarely see the EPC model giving clients the security they crave particularly for the civil works construction. Projects are often delivered late, over budget and to a poor quality standard.
The UK Construction Industry can deliver complex and challenging projects across multiple sectors but appears unable to complete less ambitious EFW projects without financial and programme failure. The EFW market for traditional Civils and Main Contractors has become Toxic and sadly for good reason.
It seems to me that the EPC model focuses too much on the process equipment that the civil works are ‘forgotten’ until it’s too late. This, in my view, simply encourages a poor project team dynamic that lacks collaboration and generates disputes throughout the whole supply chain. The client perceives it has protection from the economic cost of delay through the use of liquidated and ascertained damages (LAD’s). These are often capped leaving the client nowhere to go but to wait for the EPC to complete the project or to terminate the contract when the LAD’s run out. The irony being that the EPC price will include a LAD risk premium so the client is merely receiving the money that it paid to the EPC contractor in the first place. Or if the EPC contractor doesn’t have enough risk priced in, they simply walk away or go bust causing enormous problems for the project.
Chilworth often gets challenged on how civils risk is managed in an EPCM project structure. The mindset of offloading the construction delivery to a single contractor is anathema to EPCM contracts. EPCM requires a fully collaborative approach that puts the project first at all times. We manage risk by putting it to those that are best able to bear it and with a fully transparent structure that puts the project at the forefront rather than the contractual parties, gives the client greater control over delivery, more control over time schedules, reduces risk premiums and is a more economical solution. EPCM immediately breaks down barriers and reduces the prospect of elongated and expensive claims as everyone is simply working for the same team.
Traditional EFW’s are constructed with a crucial interrelationship of the civils with the process installation. You simply cannot have one without the other and you cannot treat them in isolation, the interface is too important. A traditionally built EFW requires the initial civil work substructures to be constructed first then the process installation commences, usually the main boiler. The civil works continue in parallel, keeping ahead of the process until the process commissioning phase when the civils is complete. Interfaces, process to process, civils to civils and process to civils as well as others have to be dealt with.
There is a perception that construction interfaces in EPCM create a risk that is difficult to mitigate for the client and stakeholders. In EPC this interrelationship is not readily seen by the client but is felt through project delays. In EPCM the interfaces are transparent from the design phase and, when identified early, are managed to ensure the right solution is obtained so that the risk rarely comes to fruition through construction. If a problem does arise it is instantly known to the team in EPCM and dealt with immediately thus mitigating it as quickly as it arose.
The advantages to the client of understanding where the construction process is in the time schedule and being able to influence the schedule, if needs be, cannot be underestimated.
We give the project stakeholders influence and control of all the components that go into development and delivery of a project. And with the right professional partners it gives the project the flexibility to be agile and move with the market to deliver the best possible design and construction solution, particularly for the civils component.
Key EPCM Takeaways
- EPCM gives transparency and control of the entire project through collaboration and flexibility.
- Risk is distributed to the party most able to bear it whilst removing an adversarial contracting culture.
- Programme certainty improves whilst lowering the construction capex.
- Design and construction expertise are engaged at all levels of the supply chain to the advantage of the project, client and stakeholders rather than the EPC or main civils work contractor.
EPCM puts the project first every time.